El bronce es una aleación a base de cobre. Los metales auxiliares pueden ser níquel, zinc, estaño, aluminio y otros. En este artículo, consideraremos tipos, características tecnológicas, químicas. la composición del bronce, así como los métodos para su fabricación.
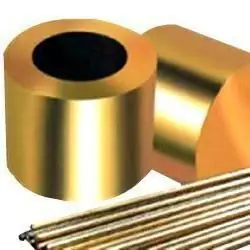
Clasificación
1. Según la composición química, este metal se suele dividir en dos grupos. El primero son los bronces al estaño. En ellos, el estaño es el principal elemento de aleación. El segundo es sin estaño. Hablaremos de esto con más detalle a continuación.
2. De acuerdo con las características tecnológicas del bronce, se acostumbra dividirlo en deformable y de fundición. Los primeros están bien procesados bajo presión. Estos últimos se utilizan para piezas moldeadas.
Este metal, en comparación con el latón, tiene propiedades mecánicas y antifricción mucho mejores, así como resistencia a la corrosión. De hecho, el bronce es una aleación de cobre y estaño (como principal elemento auxiliar). El níquel y el zinc no son aquí los principales elementos de aleación, para ello se utilizan componentes como el aluminio, el estaño, el manganeso, el silicio, el plomo, el hierro, el berilio, el cromo, el fósforo, el magnesio, el circonio y otros.
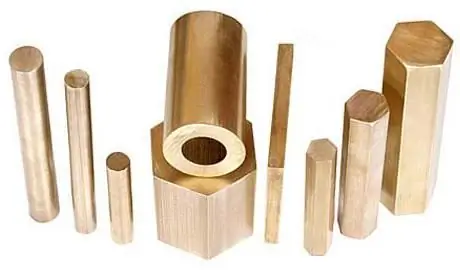
Bronces de estaño: Fundición
Averigüemos qué es ese metal. El bronce al estaño (la foto de abajo muestra piezas fundidas) es una aleación que tiene una fluidez menor que otros tipos. Sin embargo, tiene una contracción volumétrica insignificante, lo que permite obtener piezas moldeadas de bronce. Estas propiedades determinan el uso activo del bronce en la fundición de piezas antifricción. Asimismo, la aleación considerada se utiliza en la fabricación de accesorios destinados a funcionar en medio acuoso (incluida el agua de mar) o en vapor de agua, en aceites ya alta presión. También existen los llamados bronces de fundición no estándar para fines responsables. Se utilizan en la producción de cojinetes, engranajes, bujes, piezas de bombas, anillos de sellado. Estas piezas están diseñadas para operar bajo alta presión, altas velocidades y bajas cargas.
Bronces al plomo
Esta subespecie de aleaciones de estaño para fundición se utiliza en la fabricación de cojinetes, sellos y piezas moldeadas. Dichos bronces se caracterizan por sus bajas propiedades mecánicas, por lo que, en el proceso de fabricación de cojinetes y casquillos, simplemente se aplican a una base de acero en forma de una capa muy delgada. Las aleaciones con un alto contenido de estaño tienen propiedades mecánicas más altas. Por lo tanto, se pueden utilizar sin respaldo de acero.

Bronces al estaño: Deformables
Las aleaciones procesadas por presión se suelen dividir en los siguientes grupos:estaño-fósforo, estaño-zinc y estaño-zinc-plomo. Han encontrado su aplicación en la industria de la pulpa y el papel (se fabrican redes con ellos) y en la ingeniería mecánica (la producción de resortes, cojinetes y piezas de máquinas). Además, estos materiales se utilizan en la fabricación de productos bimetálicos, varillas, cintas, flejes, engranajes, engranajes, bujes y juntas para máquinas de alta carga, tubos para instrumentación, resortes de presión. En ingeniería eléctrica, el uso generalizado del bronce (forjado) se debe a sus excelentes propiedades mecánicas (junto con altas características eléctricas). Se utiliza en la fabricación de resortes portadores de corriente, conectores de enchufe, contactos. En la industria química, los bronces al estaño se utilizan para producir alambre para muelles, en mecánica de precisión - accesorios, en la industria papelera - raspadores, en la industria automotriz y de tractores - bujes y cojinetes.
Estas aleaciones se pueden suministrar en estado extraduro, duro, semiduro y blando (recocido). Los bronces al estaño suelen trabajarse en frío (laminados o trefilados). El metal caliente solo se prensa. Bajo presión, el bronce se trabaja perfectamente tanto en frío como en caliente.
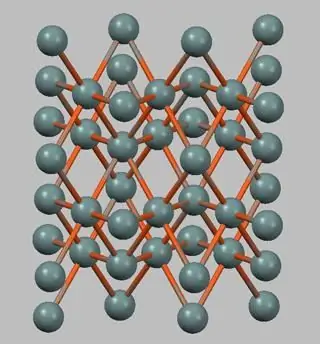
Bronce de berilio
Esta es una aleación que pertenece al grupo de metales de endurecimiento por precipitación. Tiene altas propiedades mecánicas, físicas y elásticas. El bronce de berilio tiene un alto nivel de resistencia al calor, resistencia a la corrosión y resistencia cíclica. Es resistente a bajastemperatura, no magnetiza y no da chispas cuando se golpea. El endurecimiento de los bronces de berilio se lleva a cabo a temperaturas de 750-790 grados centígrados. La adición de cob alto, hierro y níquel contribuye a ralentizar la velocidad de las transformaciones de fase durante el tratamiento térmico, lo que facilita enormemente la tecnología de envejecimiento y endurecimiento. Además, la adición de níquel contribuye a aumentar la temperatura de recristalización, y el manganeso puede reemplazar, aunque no completamente, al costoso berilio. Las características anteriores del bronce hacen posible el uso de esta aleación en la fabricación de resortes, piezas de resortes y membranas en la industria relojera.
Una aleación de cobre y manganeso
Este bronce tiene altas propiedades mecánicas especiales. Se procesa por presión, tanto en frío como en caliente. Este metal se caracteriza por una alta resistencia al calor, así como a la corrosión. Una aleación de cobre con la adición de manganeso ha encontrado una amplia aplicación en accesorios de hornos.
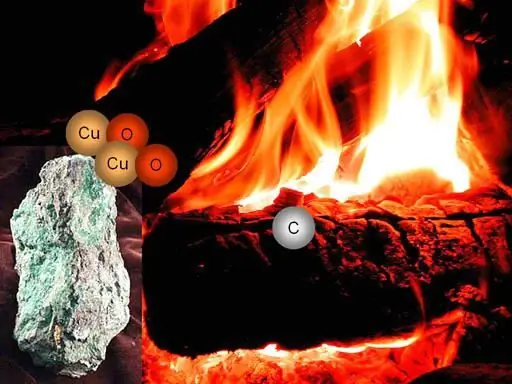
Bronce de silicio
Esta es una aleación que contiene níquel, con menos frecuencia manganeso. Tal metal se caracteriza por propiedades mecánicas, antifricción y elásticas ultra altas. Al mismo tiempo, el bronce al silicio no pierde su plasticidad a bajas temperaturas. La aleación está bien soldada, procesada por presión a altas y bajas temperaturas. El metal en cuestión no está magnetizado, no chispea cuando se golpea. Esto explica el uso generalizado del bronce (silicio) en la construcción naval marina en la fabricación de piezas antifricción, cojinetes, resortes,rejillas, evaporadores, mallas y casquillos guía.
Fundición de aleaciones sin estaño
Este tipo de bronce se caracteriza por sus buenas propiedades anticorrosivas y antifricción, así como por su alta resistencia. Se utilizan para la fabricación de piezas que se operan en condiciones particularmente difíciles. Estos incluyen engranajes, válvulas, casquillos, engranajes para potentes turbinas y grúas, tornillos sin fin que funcionan en conjunto con piezas de acero endurecido, cojinetes que funcionan bajo alta presión y cargas de choque.
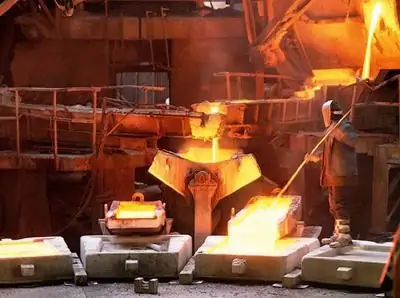
¿Cómo hacer bronce?
La producción de este metal debe realizarse en hornos especiales utilizados para la fundición de aleaciones de cobre. La carga de bronce se puede hacer a partir de metales frescos o con la adición de desechos secundarios. El proceso de fusión generalmente se lleva a cabo bajo una capa de fundente o carbón vegetal.
El proceso que usa una carga de metales frescos ocurre en una secuencia determinada. Primero, la cantidad requerida de fundente o carbón se carga en un horno altamente calentado. Luego se coloca cobre allí. Después de esperar a que se derrita, aumente la temperatura de calentamiento a 1170 grados. Después de eso, la masa fundida debe desoxidarse, para lo cual se agrega cobre fósforo. Este proceso se puede realizar en dos etapas: directamente en el horno y luego en la cuchara. En este caso, el aditivo se introduce en proporciones iguales. A continuación, los elementos de aleación necesarios calentados a 120 grados se agregan a la masa fundida. Los componentes refractarios deben introducirse en forma de ligaduras. Más bronce fundido (foto,a continuación, demuestra el proceso de fundición) se agita hasta que todas las sustancias añadidas se disuelven por completo y se calientan a la temperatura deseada. Al salir del horno la aleación resultante, antes del vertido, debe ser finalmente desoxidada con el resto (50%) de cobre fósforo. Esto se hace para liberar el bronce de los óxidos y aumentar la fluidez de la masa fundida.
Fundición a partir de materiales reciclados
Para fabricar bronce con metales y residuos reciclados, la fusión debe realizarse en el siguiente orden. Primero, el cobre se funde y se desoxida con aditivos de fósforo. Luego, los materiales circulantes se agregan a la masa fundida. Después de eso, los metales se funden por completo y los elementos de aleación se introducen en la secuencia adecuada. En el caso de que la carga consista en una pequeña cantidad de cobre puro, primero es necesario fundir los metales circulantes y luego agregar cobre y elementos de aleación. La fusión se lleva a cabo bajo una capa de fundente o carbón vegetal.
Después de fundir la mezcla y calentarla a la temperatura requerida, se realiza la desoxidación final de la mezcla con cobre fósforo. A continuación, la masa fundida se cubre con carbón calcinado o fundente seco. El consumo de este último es del 2-3 por ciento en peso del metal. La masa fundida calentada se mantiene durante 20-30 minutos, se agita periódicamente y luego se elimina la escoria separada de su superficie. Todo, el bronce está listo para la fundición. Para una mejor eliminación de la escoria, se puede agregar arena de cuarzo a la cuchara, que la espesa. Para determinar si el bronce está listo para colarse en moldes, se requiere unprueba tecnológica. La fractura de dicha muestra debe ser uniforme y limpia.
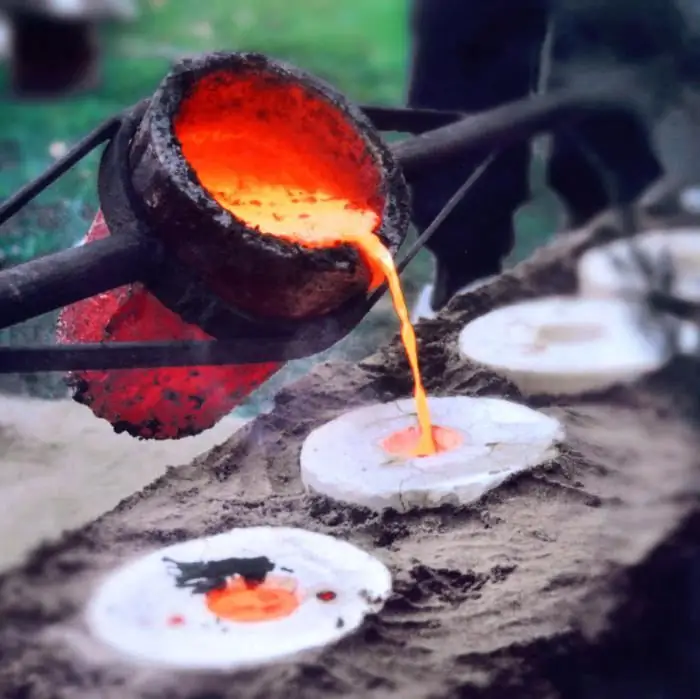
Aluminio Bronce
Es una aleación de cobre y aluminio como elemento de aleación. El proceso de fusión de este metal difiere significativamente del anterior, lo que se explica por las características químicas del componente auxiliar. Considere cómo hacer bronce usando componentes de aleación de aluminio. En la fabricación de este tipo de aleaciones utilizando materiales reciclados en la carga, no se utiliza la operación de desoxidación con componentes fosforados. Esto se debe a que el fósforo se caracteriza por una menor afinidad por las moléculas de oxígeno que el aluminio. También debes tener en cuenta que este tipo de bronce es muy sensible al sobrecalentamiento, por lo que la temperatura no debe superar los 1200 grados. En un estado sobrecalentado, el aluminio se oxida y la aleación de bronce se satura con gases. Además, el óxido formado durante la fusión de este tipo de bronce no se reduce por la adición de desoxidantes, y es muy difícil eliminarlo de la masa fundida. La película de óxido tiene un punto de fusión muy alto, lo que reduce significativamente la fluidez del bronce y provoca rechazo. La fusión se lleva a cabo de forma muy intensa, en los límites superiores de las temperaturas de calentamiento. Además, la masa fundida acabada no debe quedar retenida en el horno. Al fundir bronce al aluminio, se recomienda utilizar un fundente compuesto por un 50 % de carbonato de sodio y un 50 % de criolita como capa de cobertura.
La masa fundida terminada se refina antes de verterla en los moldes introduciendo cloruro de manganeso en ella, ocloruro de zinc (0,2-0,4% de la masa total de la carga). Después de este procedimiento, la aleación debe conservarse durante cinco minutos hasta el cese completo de la evolución del gas. Después de eso, la mezcla se lleva a la temperatura requerida y se vierte en moldes.
Para evitar la segregación en una fusión de bronce con un alto contenido de impurezas de plomo (50-60%), se recomienda agregar 2-2,3% de níquel en forma de ligaduras de cobre-níquel. O, como fundentes, es necesario utilizar la sal de sulfato de metales alcalinos. El níquel, la plata y el manganeso, si forman parte del bronce, deben introducirse en la masa fundida antes del procedimiento de adición de estaño. Además, para mejorar la calidad de la aleación resultante, a veces se modifica con aditivos menores a base de metales refractarios.