Actualmente, el torno es muy conocido. La historia de su creación comienza en los años 700 d. C. Los primeros modelos se utilizaron para trabajar la madera, 3 siglos después se creó una máquina para trabajar los metales.
Primeras menciones
En los años 700 d. C. se creó una unidad que se asemeja parcialmente a un torno moderno. La historia de su primer lanzamiento exitoso comienza con el procesamiento de madera por el método de rotación de la pieza de trabajo. Ni una sola parte de la instalación estaba hecha de metal. Por lo tanto, la fiabilidad de estos dispositivos es bastante baja.
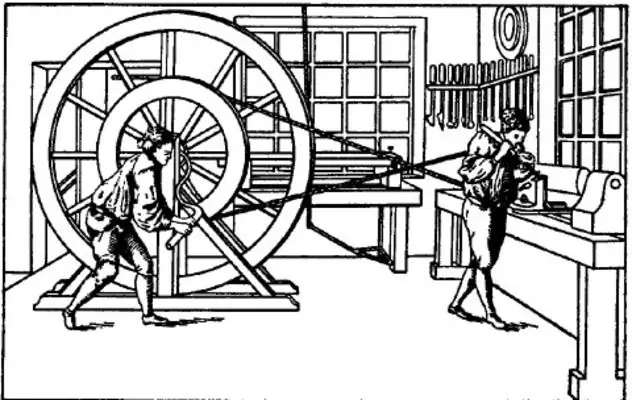
En ese momento, el torno tenía una baja eficiencia. La historia de la producción ha sido restaurada de acuerdo con los dibujos y dibujos conservados. Para desenrollar la pieza de trabajo, se requerían 2 aprendices fuertes. La precisión de los productos resultantes no es alta.
Información sobre las instalaciones, que recuerdan vagamente a un torno, la historia se remonta al año 650 a. mi. Sin embargo, estas máquinas solo tenían en común el principio de procesamiento: el método de rotación. El resto de los nodos eran primitivos. La pieza de trabajo se puso en movimiento en el verdadero sentido de la palabra. Se utilizó mano de obra esclava.
Los modelos creados en el siglo XII ya tenían una apariencia de unidad y podían obtener un producto completo. Sin embargo, todavía no había portaherramientas. Por lo tanto, era demasiado pronto para hablar de la alta precisión del producto.
El dispositivo de los primeros modelos
Un torno viejo sujetó una pieza de trabajo entre centros. La rotación se realizó a mano durante solo unas pocas revoluciones. El corte se realizó con una herramienta estacionaria. Un principio de procesamiento similar está presente en los modelos modernos.
Como motor para la rotación de la pieza de trabajo, los artesanos utilizaron: animales, un arco con flechas atado con una cuerda al producto. Algunos artesanos construyeron una especie de molino de agua para estos fines. Pero no hubo una mejora significativa en el rendimiento.
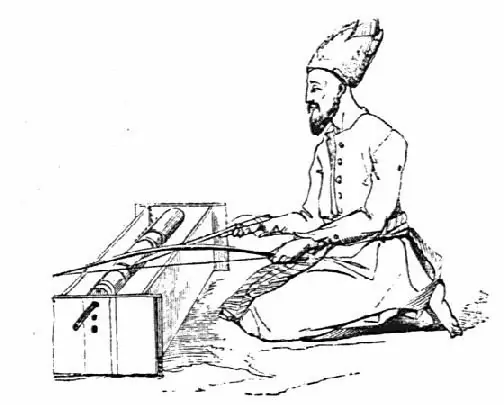
El primer torno tenía piezas de madera y, a medida que aumentaba el número de nodos, se perdía la fiabilidad del dispositivo. Los dispositivos de agua perdieron rápidamente su relevancia debido a la complejidad de la reparación. Solo en el siglo XIV apareció la unidad más simple, que simplificó enormemente el proceso de procesamiento.
Primeros actuadores
Han pasado varios siglos desde la invención del torno hasta la implementación del mecanismo de accionamiento más simple en él. Puede imaginarlo en forma de poste fijado en el medio en el marco en la parte superior de la pieza de trabajo. Un extremo de la ochepa se ata con una cuerda que se enrolla alrededor de la pieza de trabajo. El segundo se fija con un pedal.
Este mecanismo funcionó correctamente, pero no pudo proporcionar la información necesariaactuación. El principio de funcionamiento se basó en las leyes de la deformación elástica. Cuando se presionó el pedal, la cuerda se tensó, el poste se dobló y experimentó una tensión significativa. Este último se transfirió a la pieza de trabajo, poniéndola en movimiento.
Habiendo girado el producto 1 o 2 vueltas, el poste se soltó y se volvió a doblar. Con un pedal, el maestro regulaba el funcionamiento constante del oche, obligando a la pieza a girar continuamente. Al mismo tiempo, las manos estaban ocupadas con la herramienta, procesando la madera.
Este mecanismo más simple fue heredado por las siguientes versiones de máquinas que ya tenían un mecanismo de manivela. Posteriormente, las máquinas de coser mecánicas del siglo XX tenían un diseño de accionamiento similar. En tornos, con la ayuda de una manivela, lograban un movimiento uniforme en una dirección.
Debido al movimiento uniforme del maestro comenzó a recibir productos de la forma cilíndrica correcta. Lo único que f altaba era la rigidez de los nodos: centros, portaherramientas, mecanismo de accionamiento. Los soportes de los cortadores estaban hechos de madera, por lo que se escurrían durante el procesamiento.
Pero, a pesar de las deficiencias enumeradas, fue posible producir incluso piezas esféricas. La metalurgia seguía siendo un proceso difícil. Incluso las aleaciones blandas por rotación no cedieron al torneado real.
Un desarrollo positivo en el diseño de máquinas herramienta fue la introducción de la versatilidad en el procesamiento: las piezas de trabajo de varios diámetros y longitudes ya se procesaban en una sola máquina. Esto se logró mediante soportes y centros ajustables. Sin embargo, los detalles grandes requerían importantesel costo físico del asistente para implementar la rotación.
Muchos artesanos han adaptado un volante de inercia hecho de hierro fundido y otros materiales pesados. Utilizando la fuerza de la inercia y la gravedad facilitó el trabajo del manipulador. Sin embargo, todavía era difícil lograr una escala industrial.
Piezas de metal
La tarea principal de los inventores de las máquinas herramienta fue aumentar la rigidez de los nodos. El comienzo del reequipamiento técnico fue el uso de centros de metal para sujetar la pieza de trabajo. Posteriormente, ya se introdujeron los engranajes fabricados con piezas de acero.
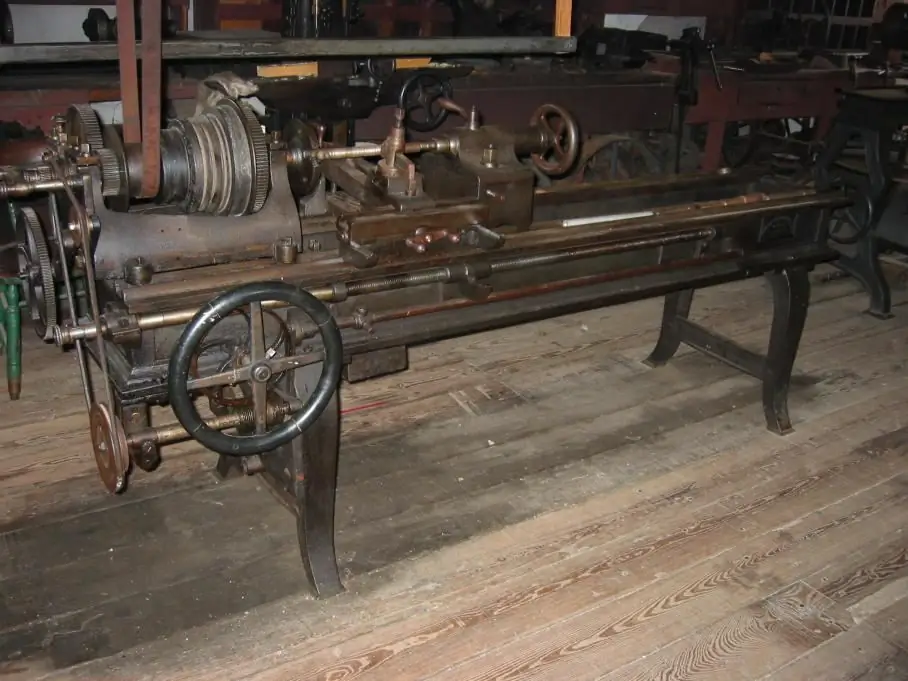
Las piezas de metal hicieron posible la creación de máquinas cortadoras de tornillos. La rigidez ya era suficiente para procesar metales blandos. Las unidades individuales se mejoraron gradualmente:
- soporte en blanco, más tarde llamado unidad principal - eje;
- los topes cónicos fueron equipados con mecanismos ajustables para cambiar la posición a lo largo;
- el trabajo de torneado se hizo más fácil con la invención del portaherramientas de metal, pero se requería una evacuación constante de virutas para aumentar la productividad;
- La cama de hierro fundido aumentó la rigidez de la estructura, lo que hizo posible procesar piezas de considerable longitud.
Con la introducción de nudos metálicos, se vuelve más difícil desenrollar la pieza de trabajo. Los inventores pensaron en crear una unidad completa, queriendo eliminar el trabajo manual humano. El sistema de transmisión ayudó a llevar a cabo el plan. La máquina de vapor se adaptó por primera vez para rotar piezas de trabajo. Fue precedido por un motor de agua.
Uniformidad de movimiento del cortela herramienta fue realizada por un engranaje helicoidal usando un mango. Esto resultó en una superficie más limpia de la pieza. Los bloques intercambiables hicieron posible realizar un trabajo universal en un torno. Las estructuras mecanizadas han mejorado a lo largo de los siglos. Pero hasta el día de hoy, el principio de funcionamiento de los nodos se basa en los primeros inventos.
Inventores científicos
Actualmente, al comprar un torno, primero se analizan las especificaciones técnicas. Proporcionan las principales posibilidades en procesamiento, dimensiones, rigidez, velocidad de producción. Anteriormente, con la modernización de los nodos, se introdujeron gradualmente parámetros según los cuales los modelos se comparaban entre sí.
Clasificación de máquinas ayudó a evaluar el grado de perfección de una máquina en particular. Después de analizar los datos recopilados, Andrei Nartov, un inventor doméstico de la época de Pedro el Grande, actualizó los modelos anteriores. Su creación fue una máquina mecanizada real que le permite realizar varios tipos de procesamiento de cuerpos de rotación, hilos cortados.
Una ventaja en el diseño de Nartov fue la capacidad de cambiar la velocidad de rotación del centro móvil. También proporcionaron bloques de engranajes intercambiables. La apariencia de la máquina y el dispositivo se asemejan a un torno simple moderno TV3, 4, 6. Los centros de mecanizado modernos tienen unidades similares.
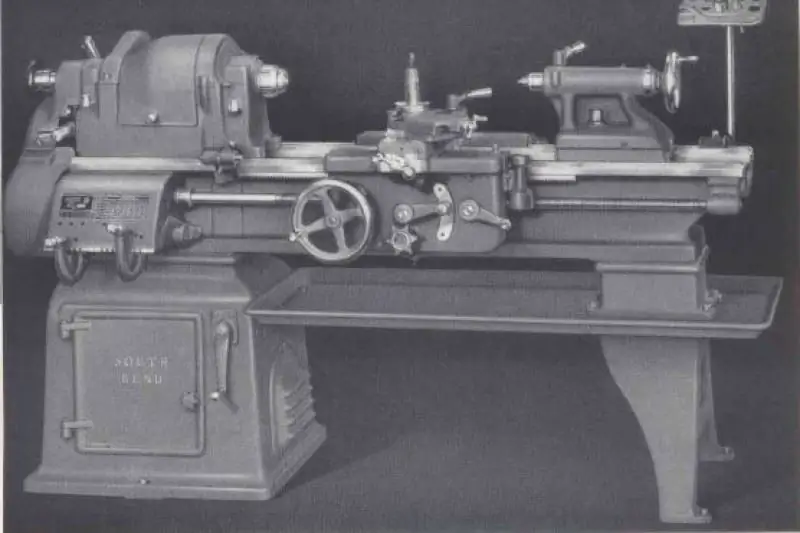
En el siglo XVIII, Andrey Nartov presentó al mundo la pinza autopropulsada. El tornillo de avance transmitió el movimiento uniforme de la herramienta. Henry Maudsley, inventor inglés, presentó suversión de un nodo importante a finales de siglo. En su diseño, el cambio en la velocidad de movimiento de los ejes se realizó debido al diferente paso de rosca del husillo.
Nudos principales
Los tornos son ideales para tornear piezas en 3D. Una descripción general de una máquina moderna contiene los parámetros y características de los componentes principales:
- Bed - el principal elemento cargado, el marco de la máquina. Hecha de aleaciones duraderas y duras, se utiliza principalmente perlita.
- Soporte: una isla para conectar cabezales de herramientas giratorios o una herramienta estática.
- Husillo: actúa como soporte de la pieza de trabajo. El poderoso nudo de rotación principal.
- Unidades adicionales: husillos de bolas, ejes deslizantes, mecanismos de lubricación, suministro de refrigerante, purgadores de aire del área de trabajo, enfriadores.
Un torno moderno contiene sistemas de accionamiento que consisten en una electrónica de control sofisticada y un motor, a menudo síncrono. Las opciones adicionales le permiten eliminar virutas del área de trabajo, medir la herramienta, suministrar refrigerante bajo presión directamente al área de corte. La mecánica de la máquina se selecciona individualmente para las tareas de producción, y el costo del equipo también depende de esto.
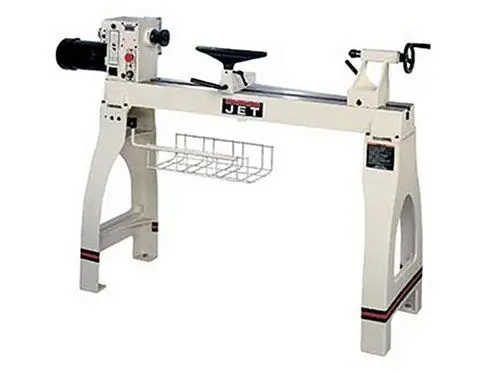
La pinza contiene nodos para colocar rodamientos que están montados en el husillo de bolas (par de husillos de bolas). Además, se montan elementos para el contacto con las guías deslizantes. La lubricación en las máquinas modernas se suministra automáticamente, se controla su nivel en el tanque.
En los primeros tornos, movimientola herramienta fue realizada por una persona, eligió la dirección de su movimiento. En los modelos modernos, todas las manipulaciones son realizadas por el controlador. Se necesitaron varios siglos para la invención de tal nudo. La electrónica ha ampliado enormemente las capacidades de procesamiento.
Gestión
Recientemente, los tornos de metal CNC se han generalizado, con control numérico. El controlador controla el proceso de corte, monitorea la posición de los ejes, calcula el movimiento de acuerdo con los parámetros establecidos. La memoria almacena varias etapas de corte, hasta la salida de la pieza terminada.
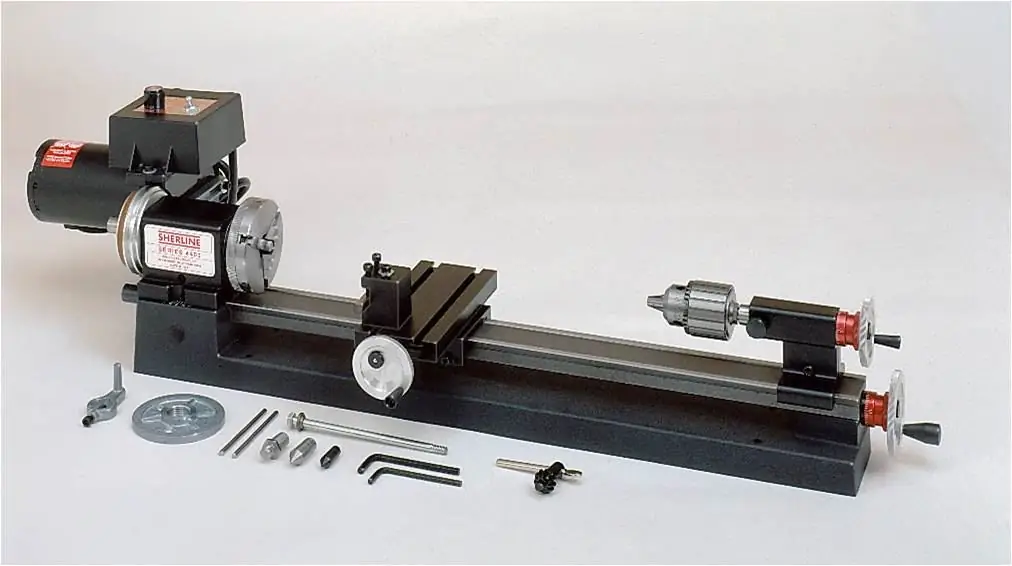
Los tornos de metal CNC pueden tener visualización de procesos, lo que ayuda a verificar el programa escrito antes de que la herramienta se mueva. Todo el corte se puede ver virtualmente y los errores de código se pueden corregir a tiempo. La electrónica moderna controla la carga por eje. Las últimas versiones del software le permiten identificar una herramienta rota.
La metodología para el control de plaquitas rotas en el portaherramientas se basa en comparar la curva de carga del eje durante el funcionamiento normal y cuando se supera el umbral de emergencia. El seguimiento ocurre en el programa. La información para el análisis se proporciona al controlador mediante un sistema de accionamiento o un sensor de potencia con la capacidad de digitalizar valores.
Sensores de posición
Las primeras máquinas con electrónica tenían finales de carrera con microinterruptores para controlar las posiciones extremas. Más tarde, se instalaron codificadores en la hélice. Actualmente se utilizan reglas de alta precisión que pueden medir unas pocas micras de juego.
Equipado con sensores circulares y ejes de rotación. El conjunto del husillo podría controlarse. Esto es necesario para implementar las funciones de fresado realizadas por la herramienta accionada. Este último a menudo se construía en la torreta.
La integridad de la herramienta se mide mediante sondas electrónicas. También facilitan la búsqueda de puntos de anclaje para iniciar el ciclo de corte. Las sondas pueden medir la geometría de los contornos obtenidos de la pieza después del procesamiento y automáticamente hacer correcciones que se incluyen en el re-acabado.
El modelo moderno más sencillo
El torno TV 4 es un modelo de entrenamiento con el mecanismo de accionamiento más simple. Todo el control es manual.
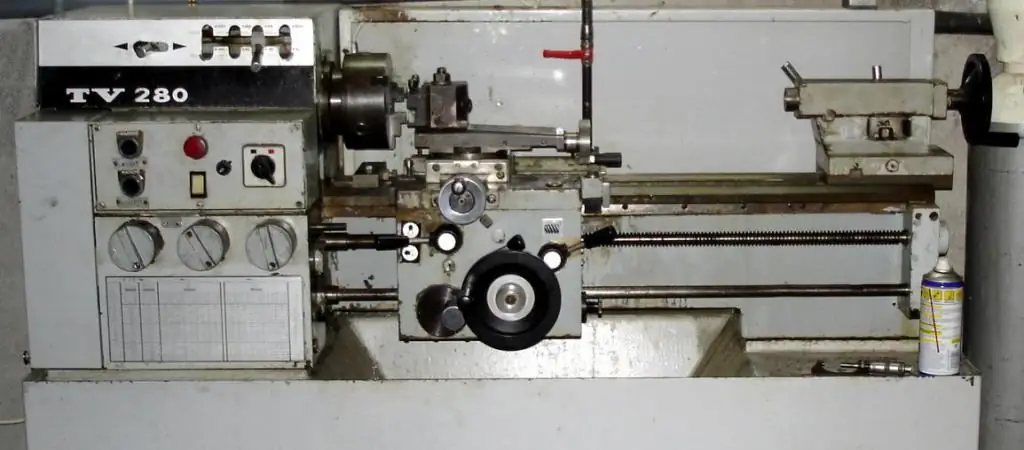
Mangos:
- ajustar la posición de la herramienta en relación con el eje de rotación;
- establece la dirección de enhebrado a la derecha o a la izquierda;
- se utilizan para cambiar la velocidad de la unidad principal;
- determinar el paso de rosca;
- incluye el movimiento longitudinal de la herramienta;
- se encargan de sujetar los nudos: el contrapunto y sus púas, cabezas con incisivos.
Los volantes mueven nodos:
- pluma de contrapunto;
- carro longitudinal.
El diseño proporciona un circuito de iluminación para el área de trabajo. Una pantalla de seguridad en forma de pantalla protectora protege a los trabajadores de las virutas. El diseño de la máquina es compacto, lo que permite su uso en aulas, salas de servicio.
El torno cortador de tornillos TV4 es un simpleestructuras, donde se proporcionan todos los componentes necesarios de una estructura de procesamiento de metal en toda regla. El husillo es accionado a través de una caja de cambios. La herramienta está montada sobre un soporte con avance mecánico, accionado por un par de tornillos.
Tamaños
El husillo es accionado por un motor asíncrono. El tamaño máximo de la pieza de trabajo puede ser de diámetro:
- no más de 125 mm si se mecaniza sobre el calibrador;
- no más de 200 mm si el mecanizado se realiza sobre la bancada.
La longitud de la pieza de trabajo sujeta en los centros no supera los 350 mm. La máquina ensamblada pesa 280 kg, la velocidad máxima del husillo es de 710 rpm. Esta velocidad de rotación es decisiva para el acabado. La alimentación se suministra desde una red de 220 V con una frecuencia de 50 Hz.
Características del modelo
La caja de cambios de la máquina TV4 está conectada al motor del husillo mediante una transmisión de correa trapezoidal. En el eje, la rotación se transmite desde la caja a través de una serie de engranajes. La dirección de rotación de la pieza de trabajo se cambia fácilmente poniendo en fase el motor principal.
La guitarra se usa para transferir la rotación del husillo a las pinzas. Es posible cambiar 3 velocidades de alimentación. En consecuencia, se cortan tres tipos diferentes de hilos métricos. El husillo asegura un recorrido suave y uniforme.
Las manijas establecen la dirección de rotación del par de hélices del cabezal. Los mangos también establecen las velocidades de avance. La pinza solo se mueve en dirección longitudinal. Los conjuntos deben lubricarse manualmente de acuerdo con las normas de la máquina. Los engranajes, por otro lado, toman grasa del baño en el que trabajan.
En la máquinala capacidad de trabajar manualmente. Los volantes se utilizan para esto. La cremallera y el piñón engranan con la cremallera y el piñón. Este último está atornillado al marco. Este diseño permite, si es necesario, incluir el control manual de la máquina. Se utiliza un volante similar para mover la caña del contrapunto.