El hierro es un elemento familiar para todas las personas de nuestro planeta. Y no hay nada sorprendente en esto. De hecho, en cuanto a su contenido en la corteza terrestre (hasta un 5%), este componente es el más común. Sin embargo, sólo una cuadragésima parte de estas reservas se encuentran en yacimientos aptos para el desarrollo. Los principales minerales de hierro son siderita, mineral de hierro marrón, hematita y magnetita.
Origen del nombre
¿Por qué el hierro tiene este nombre? Si consideramos la tabla de elementos químicos, en ella este componente está marcado como "ferrum". Se abrevia Fe.
Según muchos etimólogos, la palabra "hierro" nos llegó del idioma protoeslavo, en el que sonaba como zelezo. Y este nombre vino del léxico de los antiguos griegos. Llamaron al metal tan famoso hoy en día "hierro".
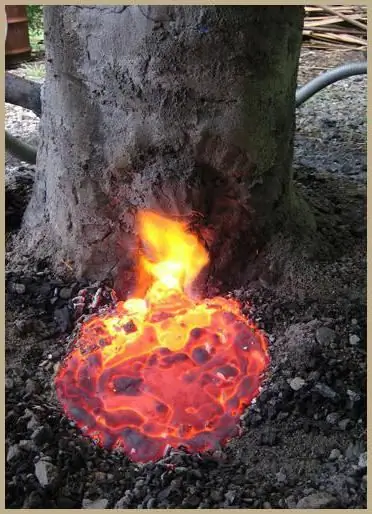
Hay otra versión. Según ella, el nombre "hierro" nos llegó del latín, dondesignificaba "estrellado". La explicación de esto radica en el hecho de que las primeras muestras de este elemento descubiertas por la gente eran de origen meteorito.
Uso del hierro
En la historia de la humanidad, hubo un período en el que la gente valoraba más el hierro que el oro. Este hecho está registrado en la Odisea de Homero, que dice que a los ganadores de los juegos dispuestos por Aquiles se les daba, además de oro, una pieza de hierro. Este metal era esencial para casi todos los artesanos, agricultores y guerreros. Y fue la enorme necesidad que se convirtió en el mejor motor para la producción de este material, así como un mayor progreso técnico en su fabricación.
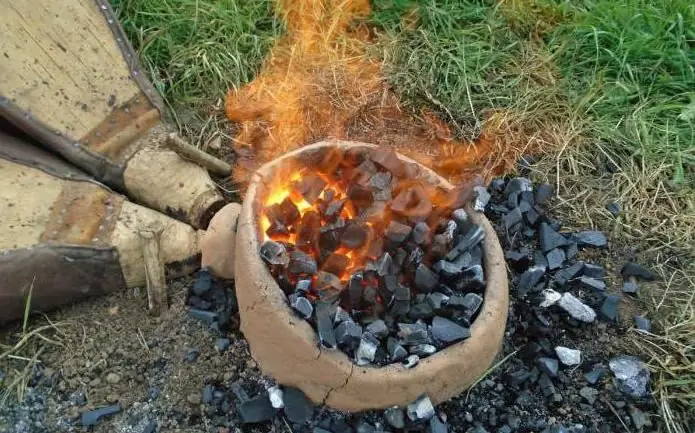
9-7 cc. ANTES DE CRISTO. considerada la Edad del Hierro en la historia humana. Durante este período, muchas tribus y pueblos de Asia y Europa comenzaron a desarrollar la metalurgia. Sin embargo, el hierro todavía tiene una gran demanda en la actualidad. Después de todo, sigue siendo el principal material utilizado para la fabricación de herramientas.
Producto de queso
¿Cuál es la tecnología para producir hierro fundido que la humanidad comenzó a extraer en los albores del desarrollo de la metalurgia? El primer método inventado por la humanidad se llamó elaboración de queso. Además, se usó durante 3000 años, sin cambios desde el final de la Edad del Bronce hasta el período hasta el siglo XIII. El alto horno no se inventó en Europa. Este método se llamó crudo. Los cuernos para él fueron construidos de piedra o arcilla. A veces pedazos de escoria actuaban como material para sus paredes. La última versión de la fragua desde el interior fuerevestido con arcilla refractaria, a la que se le añadía arena o cuerno triturado para mejorar la calidad.
¿Qué hace el flash iron? Los pozos preparados se llenaron con mineral de pradera o pantano "en bruto". El espacio de fusión de tales hornos se llenaba con carbón vegetal, que luego se calentaba completamente. En el fondo del pozo había un agujero para el suministro de aire. Al principio, se soplaba con fuelles manuales, que luego fueron reemplazados por mecánicos.
En las primeras fraguas se organizaba el tiro natural. Se llevó a cabo a través de orificios especiales: boquillas, que se ubicaron en las paredes de la parte inferior del horno. A menudo, los antiguos metalúrgicos proporcionaban suministro de aire mediante el uso de un diseño que permitía obtener el efecto de una tubería. Crearon un espacio interior alto y al mismo tiempo estrecho. Muy a menudo, tales hornos se construyeron al pie de las colinas. Estos lugares tenían la mayor presión de viento natural, que se utilizó para aumentar la tracción.
Como resultado del proceso en curso, el mineral se convirtió en metal. Al mismo tiempo, la roca vacía fluyó gradualmente hacia abajo. Granos de hierro formados en el fondo del horno. Se pegaron entre sí, convirtiéndose en el llamado "creep". Se trata de una masa esponjosa suelta impregnada de escorias. En el horno, la galleta estaba al rojo vivo. Fue en este estado que lo sacaron y rápidamente lo falsificaron. Pedazos de escoria simplemente se cayeron. A continuación, el material resultante se soldaba en una pieza monolítica. El resultado fue hierro llamativo. El producto final tenía la forma de un pan plano.
Qué fue¿composición de la floración de hierro? Era una aleación de Fe y carbono, que era muy pequeña en el producto final (si tenemos en cuenta el porcentaje, entonces no más de centésimas).
Sin embargo, el hierro en flor que la gente recibía en el horno crudo no era muy duro ni duradero. Es por eso que los productos hechos de dicho material fallaron rápidamente. Las lanzas, las hachas y los cuchillos estaban doblados y no permanecían afilados por mucho tiempo.
Acero
En la producción de hierro en fraguas, además de sus grumos blandos, también había aquellos que tenían una mayor dureza. Estos eran pedazos de mineral que estuvieron en estrecho contacto con el carbón durante el proceso de fundición. Un hombre notó este patrón y comenzó a aumentar deliberadamente el área en contacto con el carbón. Esto hizo posible cementar el hierro. El metal resultante comenzó a satisfacer las necesidades de los artesanos y de quienes utilizaban productos elaborados con él.
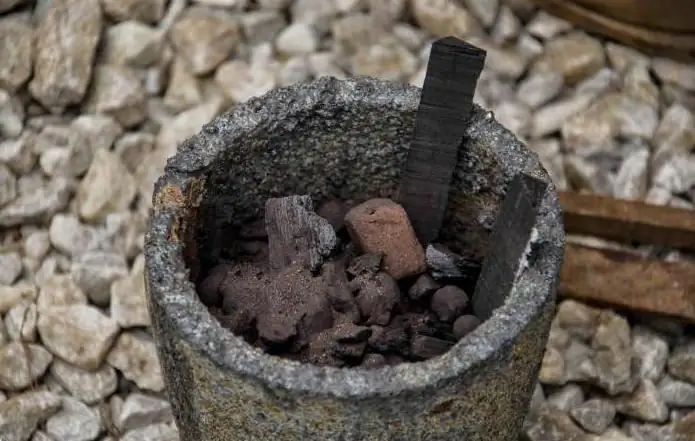
Este material era acero. Todavía se utiliza hasta el día de hoy en la fabricación de una gran cantidad de estructuras y productos. El acero, fundido por antiguos metalúrgicos, es hierro fundido, que contiene hasta un 2 % de carbono.
También existía el acero dulce. Era flash iron, que contenía menos del 0,25% de carbono. Si consideramos la historia de la metalurgia, entonces fue el acero dulce el que se produjo en la etapa inicial de la producción de queso. ¿Cuál es otro nombre para el flash iron? También hay una tercera variedad. Cuando contiene más del 2% de carbono, entonceses de hierro fundido.
Invención del alto horno
El floreciente método para obtener hierro usando forjas puras dependía en gran medida del clima. Después de todo, para tal tecnología era importante que el viento soplara dentro del tubo fabricado. Fue el deseo de alejarse de los caprichos del clima lo que llevó a una persona a crear pieles. Estos eran los dispositivos necesarios para avivar el fuego en el horno crudo.
Después de la aparición de los fuelles, las fraguas para la producción de metales ya no se construyeron en las laderas. La gente comenzó a usar un nuevo tipo de estufas, llamadas "focos de lobo". Eran estructuras, una parte de las cuales estaba en el suelo, y la segunda (casas) se elevaba sobre ella en forma de una estructura hecha de piedras unidas por arcilla. En la base de tal horno había un agujero en el que se insertaba un tubo de fuelle para avivar el fuego. El carbón colocado en la casa se quemó, después de lo cual fue posible obtener la galleta. La sacaron a través del agujero, que se formó después de quitar varias piedras de la parte inferior de la estructura. A continuación, se restauró el muro y se llenó el horno con mineral y carbón para empezar de nuevo.

La producción de hierro brillante se ha mejorado constantemente. Con el tiempo, las casas comenzaron a construirse más grandes. Esto requería un aumento en la productividad de los mechs. Como resultado, el carbón comenzó a quemarse más rápido, saturando el hierro con carbón.
Hierro fundido
¿Cómo se llama la plancha con alto contenido de carbono? Como eramencionado anteriormente, este es el hierro fundido que es tan común hoy en día. Su característica distintiva es la capacidad de fundirse a temperaturas relativamente bajas.
Ladrillo de hierro - hierro fundido en forma sólida - era imposible de falsificar. Es por eso que los antiguos metalúrgicos no le prestaron atención al principio. De un solo golpe con un martillo, este material simplemente se rompió en pedazos. En este sentido, el hierro fundido, así como la escoria, se consideró inicialmente un producto de desecho. En Inglaterra, este metal incluso se llamaba "arrabio". Y solo con el tiempo, la gente se dio cuenta de que este producto, mientras está en forma líquida, se puede verter en moldes para obtener varios productos, por ejemplo, balas de cañón. Gracias a este descubrimiento en los siglos 14-15. en la industria se empezaron a construir altos hornos para la produccion de arrabio. La altura de tales estructuras alcanzó los 3 metros o más. Con su ayuda, se fundió hierro de fundición para la producción no solo de balas de cañón, sino también de los propios cañones.
Desarrollo de la producción en altos hornos
Una verdadera revolución en el negocio metalúrgico ocurrió en los años 80 del siglo XVIII. Fue entonces cuando uno de los empleados de Demidov decidió que, para una mayor eficiencia en el funcionamiento de los altos hornos, se les debe suministrar aire no a través de una, sino a través de dos boquillas, que deben ubicarse a ambos lados del hogar. Poco a poco, el número de tales boquillas creció. Esto permitió uniformar el proceso de soplado, aumentar el diámetro de la solera y aumentar la productividad de los hornos.
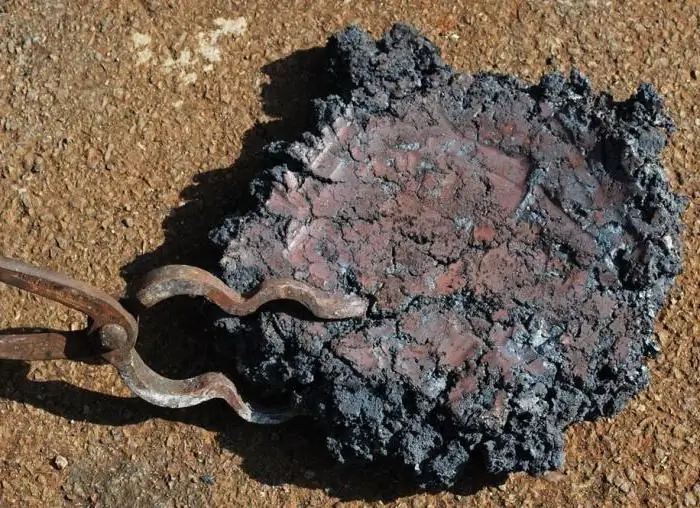
El desarrollo de la producción en altos hornos también se vio facilitado por la sustitución del carbón vegetal,por lo que se cortaron los bosques, para coque. En 1829, en Escocia, en la planta de Clayde, se insufló por primera vez aire caliente en el alto horno. Tal innovación aumentó significativamente la productividad del horno y redujo el consumo de combustible. Hoy en día, el proceso del alto horno se ha mejorado reemplazando parte del coque con gas natural, que tiene un costo aún menor.
Bulat
¿Cuál es el nombre del flash iron, que tiene propiedades únicas que se usaban en la fabricación de armas? Conocemos este material como acero de damasco. Este metal, como el acero de Damasco, es una aleación de hierro y carbono. Sin embargo, a diferencia de sus otras especies, es un hierro llamativo y con buenas cualidades. Es resistente y duro, y también capaz de producir un afilado excepcional en la hoja.
Metalúrgicos de muchos países han estado tratando de desentrañar el secreto de la producción de acero de damasco durante más de un siglo. Se propusieron una gran cantidad de recetas y métodos que incluían la adición de marfil, piedras preciosas, oro y plata al hierro. Sin embargo, el secreto del acero de damasco no fue revelado hasta la primera mitad del siglo XX por el destacado metalúrgico ruso P. P. Anosov. Tomaron hierro en flor, que se puso en un horno con carbón, donde ardía un fuego abierto. El metal fundido, saturado con carbón. En ese momento, estaba cubierto con escoria de dolomita cristalina, a veces con la adición de la más pura cascarilla de hierro. Debajo de tal capa, el metal se liberó muy intensamente del silicio, el fósforo, el azufre y el oxígeno. Sin embargo, eso no fue todo. El acero resultante tuvo que ser enfriado tanto como sea posible.más lento y más tranquilo. Esto hizo posible formar, en primer lugar, grandes cristales que tienen una estructura ramificada (dendritas). Tal enfriamiento tuvo lugar directamente en el hogar, que estaba lleno de carbón caliente. En la siguiente etapa, se llevó a cabo una forja hábil, durante la cual la estructura resultante no debería colapsar.
Las propiedades únicas del acero de damasco encontraron posteriormente una explicación en los trabajos de otro metalúrgico ruso D. K. Chernov. Explicó que las dendritas son de acero refractario pero relativamente blando. El espacio entre sus "ramas" en el proceso de solidificación del hierro se llena con más carbono saturado. Es decir, el acero blando está rodeado de acero más duro. Esto explica las propiedades del acero de damasco, contenidas en su viscosidad y al mismo tiempo de alta resistencia. Tal híbrido de acero durante la fusión conserva su estructura de árbol, convirtiéndolo solo de una línea recta a una en zigzag. La peculiaridad del patrón resultante depende en gran medida de la dirección de los golpes, la fuerza y la habilidad del herrero.
Acero de Damasco
En la antigüedad, este metal era el mismo acero de damasco. Sin embargo, un poco más tarde, el acero de Damasco comenzó a llamarse un material obtenido por soldadura forjada de una gran cantidad de alambres o tiras. Estos elementos estaban hechos de acero. Además, cada uno de ellos se caracterizó por un contenido de carbono diferente.
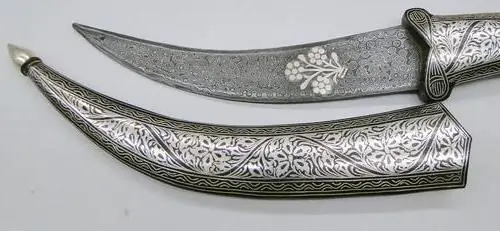
El arte de fabricar tal metal alcanzó su mayor desarrollo en la Edad Media. Por ejemplo, en la estructura de la conocida hoja japonesa, los investigadores encontraroncerca de 4 millones de hilos de acero de espesor microscópico. Esta composición hizo que el proceso de fabricación de armas fuera muy laborioso.
Producción en condiciones modernas
Los antiguos metalúrgicos dejaron una muestra de su destreza no solo en las armas. El ejemplo más llamativo de puro hierro floreado es la famosa columna situada cerca de la capital de la India. Los arqueólogos determinaron la edad de este monumento de arte metalúrgico. Resultó que la columna se construyó hace otros 1.500 años. Pero lo más sorprendente radica en el hecho de que hoy en día es imposible detectar incluso pequeños rastros de corrosión en su superficie. El material de la columna se sometió a un examen cuidadoso. Resultó que se trata de hierro flash puro, que contiene solo un 0,28 % de impurezas. Tal descubrimiento asombró incluso a los metalúrgicos modernos.
Con el tiempo, el hierro llamativo perdió gradualmente su popularidad. El metal fundido en horno abierto o alto horno comenzó a gozar de la mayor demanda. Sin embargo, al aplicar estos métodos se obtiene un producto de pureza insuficiente. Es por ello que el método más antiguo de producción de este material ha recibido recientemente su segunda vida, lo que permite producir metal con las más altas características de calidad.
¿Cómo se llama el flash iron hoy en día? Nos resulta familiar como metal de reducción directa. Por supuesto, hoy en día, el hierro florido no se produce de la misma manera que en la antigüedad. Para su producción se utilizan las tecnologías más modernas. Permiten producir metal que prácticamente no tieneimpurezas extrañas. Los hornos de tubo rotatorio se utilizan en la producción. Dichos elementos estructurales se utilizan para cocer diversos materiales a granel utilizando altas temperaturas en la industria química, del cemento y muchas otras industrias.
¿Cómo se llama ahora el flash iron? Se considera puro y se utiliza para obtener un método que, en esencia, no difiere mucho del que existía en la antigüedad. Aún así, los metalúrgicos utilizan el mineral de hierro, que se calienta en el proceso de obtención del producto final. Sin embargo, hoy en día las materias primas se someten inicialmente a un procesamiento adicional. Se enriquece creando una especie de concentrado.
La industria moderna utiliza dos métodos. Ambos te permiten obtener hierro instantáneo a partir de concentrados.
El primero de estos métodos se basa en llevar las materias primas a la temperatura requerida utilizando combustible sólido. Tal proceso es muy similar al realizado por los antiguos metalúrgicos. En lugar de combustible sólido, se puede utilizar gas, que es una combinación de hidrógeno y monóxido de carbono.
¿Qué precede a la obtención de este material? ¿Cuál es el nombre de flash iron hoy? Después de calentar el concentrado de mineral de hierro, los gránulos permanecen en el horno. De ellos se produce posteriormente el metal puro.
El segundo método utilizado para restaurar el hierro es muy similar en tecnología al primero. La única diferencia es que los metalúrgicos usan hidrógeno puro como combustible para calentar el concentrado. Con este método, el hierro se obtiene mucho más rápido. Exactamentepor lo tanto, se distingue por una mayor calidad, porque en el proceso de interacción del hidrógeno con el mineral enriquecido, solo se obtienen dos sustancias. El primero de ellos es hierro puro, y el segundo es agua. Podría suponerse que este método es muy popular en la metalurgia moderna. Sin embargo, hoy en día se usa con poca frecuencia y, por regla general, solo para la producción de polvo de hierro. Esto se explica por el hecho de que es bastante difícil obtener hidrógeno puro, tanto para resolver problemas técnicos como por dificultades económicas. El almacenamiento del combustible recibido también es una tarea difícil.
Relativamente recientemente, los científicos han desarrollado otro tercer método para la producción de hierro reducido. Se trata de la obtención de metal a partir de concentrado de mineral, sin pasar por la etapa de su transformación en pellas. Los estudios han demostrado que con este método, el hierro puro se puede producir mucho más rápido. Sin embargo, este método aún no se ha implementado en la industria, ya que requiere cambios tecnológicos importantes y un cambio en el equipamiento de las empresas metalúrgicas.
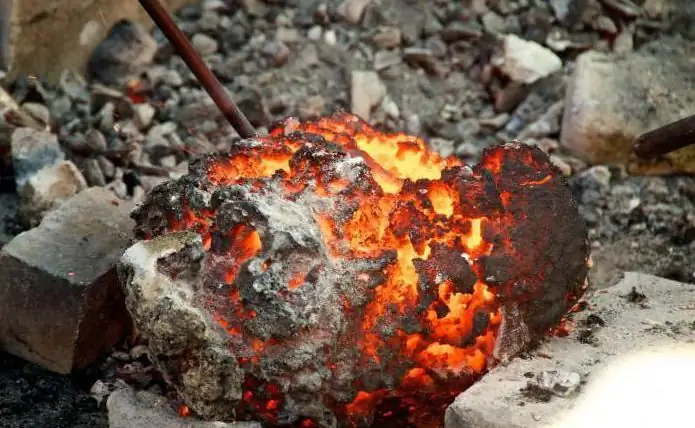
¿Cuál es el nombre de flash iron hoy? Este material nos es familiar como metal de reducción directa, a veces también se le llama esponjoso. Este es un material rentable, de alta calidad y respetuoso con el medio ambiente que no tiene impurezas de fósforo y azufre. Por sus características, el hierro bloomery se utiliza en las industrias de la ingeniería (aviación, construcción naval e instrumentación).
Fechral
Como puede ver, hoy al usarlas tecnologías más modernas utilizan material como el hierro en flor. Fechral es también una aleación codiciada. Además de hierro, contiene componentes como cromo y aluminio. El níquel también está presente en su estructura, pero no más del 0,6%.
Fechral tiene buena resistencia eléctrica, alta dureza, funciona muy bien con cerámicas con alto contenido de alúmina, no tiene tendencia a picaduras y es resistente al calor en una atmósfera que contiene azufre y sus compuestos, hidrógeno y carbono. Pero la presencia de hierro en la aleación la vuelve bastante quebradiza, lo que dificulta el procesamiento del material en la fabricación de varios productos.
Fechral se utiliza en la fabricación de elementos calefactores para hornos industriales y de laboratorio, cuya temperatura máxima de funcionamiento es de 1400 grados. A veces, las piezas de esta aleación se utilizan para otros fines. Se colocan en aparatos domésticos de calefacción, así como en aparatos eléctricos de acción térmica. Fechral ha sido ampliamente utilizado en la producción de cigarrillos electrónicos. Además, se demanda una aleación de hierro, aluminio y cromo en el campo de la fabricación de elementos resistivos. Estos pueden ser, por ejemplo, resistencias de arranque y frenado de locomotoras eléctricas.
Fechral se utiliza para producir alambre, así como hilo y cinta. A veces se obtienen círculos y varillas. Todos estos productos se utilizan en la fabricación de diversas formas de calentadores para hornos eléctricos.